The Future of Sustainable Pharma Blister Packaging
- Colin Reed
- Apr 2
- 18 min read
Further to our 2023 article on Healthcare Packaging and the Circular Economy, Reap Consulting has been diving deeper into Blister Packaging, and how regulations such as the EU PPWR, concerns around PFAS and DEHP, and changes in EPR fees will impact the use of PVC in Europe and elsewhere.
Innovations in sustainable alternatives to PVC have taken huge strides forwards since 2022, and are close to being operationally and economically viable at commercial volumes for both low- and medium-barrier applications.
What is the future of PVC in Pharmaceutical Blister Packs, and what are the alternatives?
Introduction
The PVC blister pack with its aluminium foil lid, which first appeared in 1961, has remained unchanged for more than 60 years, except for the additions of barrier coatings such as PVdC and PCTFE to improve protection and extend shelf life. Whenever Sustainability has been discussed in the past, the Pharmaceutical industry has justifiably used the arguments of patient safety, product protection, regulations and cost to avoid having to follow the path of Food and other Consumer Packaging to become more sustainable. The invention of the ultra-high barrier (alu-alu) cold form blister pack in the 1970s was a small step towards a more recyclable blister, allowing the aluminium to be recovered. However, this is only possible once the laminated plastics have been incinerated, PVC being the greatest plastic component, so sustainability gains for cold form foil are marginal.

Alternatives have existed for decades, and PP/foil blisters have been extensively used in Japan for many years. Even the cold form blister has long been available with PP or HDPE, but this has never been used for more than a small percentage of products.
Change is now in the air, and it seems that sustainable blister packaging will eventually take hold.
Summary
This white paper will identify the changes since 2020 that have led to an increased urgency within the Pharmaceutical and Packaging industries to introduce recyclable primary packaging. It will review the options available for Pharma companies to replace PVC/foil blisters, and how these compare against each other across the range of barrier requirements. It will assess the opportunities for the Pharma companies, as well as packaging suppliers, and the challenges that need to be overcome to make the introduction of PVC-free blister packs economically viable. It will go on to consider future models on the extent, timing and speed of any move away from PVC, estimating the impact on the existing supply chains and the alternative materials. Finally, it will highlight the other challenges in the process towards a circular economy, and how these may be addressed.
Drivers for Change
Since 2020, when the EU announced significant targets to make packaging recyclable and reusable, there has been great urgency across all consumer industries and packaging suppliers to meet this challenge. Despite Pharmaceuticals and Medical Devices being exempted from the EU PPWR, Consumer Health products are not. Together with a broader need for the Pharmaceutical Industry to be seen to take a more environmentally friendly approach to its business, other changes have created a drive to respond. Across Europe EPR fees are increasingly linked to positive packaging choices (eco-modulation), and health and environmental issues such as PFAS and DEHP have gained greater attention across Europe and North America. Add to that a pressure from consumers and retailers to provide recyclable packaging for OTC and Consumer Health products, and the industry has had to respond.
Several global Pharmaceutical companies have made bold statements about removing PVC from their packaging by around 2030, others have been a little less direct, but across the industry, there is a wave to identify alternatives to the PVC/foil blister and replace it with recyclable packaging.
The focus on PVC blisters
The reasons that PVC has survived for over 60 years as the material of choice for blister packs are that it is safe for humans, readily available, and easy to process. Its “only” problems are that it is difficult to dispose and recycle, due to its high chlorine and additive contents, and, whether it is incinerated or sent to landfill, it releases toxic chlorine-based chemicals. These toxins have been shown to be cause harm to human and animal health, including cancer, immune system damage, hormone disruption, infertility and impaired childhood development.
The coatings and films that are added to PVC to improve moisture and oxygen barrier are no better. PVdC is coated on PVC in various thicknesses to produce medium-barrier blisters. PVdC suffers from the same challenges as PVC, having a very high chlorine content. For the highest moisture barrier plastic blisters, PVC is also laminated with polychlorotrifluoroethylene (PCTFE - most commonly Aclar from Honeywell). PCTFE has the additional challenge of being a PFAS (per- and polyfluoroalkyl substance), which has come under even more scrutiny since 2021, more of which later.
Historical Alternatives to PVC
Whenever discussions about sustainable packaging have arisen in the past, the Pharma industry has been exempted from moving away from PVC-based blisters, due to the safety-focused regulatory environment that makes change time-consuming and expensive, and the lack of any “viable” alternatives - although this isn’t strictly true. Polypropylene (PP) has been freely available for decades, as has polyethylene terephthalate (PET), both as alternatives to low-barrier blisters – typically the larger volumes in OTC and Consumer Health applications.
PP has long had a reputation as being difficult to handle on blister packaging lines, with the need for pre-heating, change of tooling, and slower speeds, which adds critical cost to these types of medicines. PET is easier, but in both cases, the basic resins, supplied within the regulatory and quality demands of the industry, have usually been more expensive that PVC. Add to that the need for a different lidding foil specification, to enable a seal to the base film, then the increased cost and complexity have been hurdles that the industry was not ready to overcome for limited environmental gain.
Adding PVdC as a barrier coating to PET is also possible, and more sustainable barrier options were developed in the late 1990s, using cyclic olefin copolymer (COC) in various gauges sandwiched between two layers of PP, to achieve medium-to-high moisture barrier. The limited availability and higher cost of the COC, and the lack of significant benefit when combined with a foil lid has led to a minimal usage to these materials.
These specifications have extended the moisture barrier performance of the PVC-free flat sheet base film into the mid-barrier range, but the higher-barrier demands have remained the territory of PVC-based blisters with the higher thicknesses of PVdC (Super B) and PCTFE, as well as cold form foil.

Regardless of the industry’s ability to produce a sustainable base film, the lidding has almost entirely remained an aluminium foil, with push-through formats the most popular, due to the compact blister size and ease of patient use. This combination has restricted the sustainability credentials of the final blister pack, as the foil lid and plastic base cannot be separated for recycling. Although a viable push-through PP lid film had been developed by Etimex, and a PP monopolymer blister was commercially used for limited Pharma applications, this never gained broader acceptance.
Until now…
What’s different now?
As plastic consumer packaging has come under extreme pressure since 2020, and the Pharmaceutical industry has also been scrutinised for the environmental impact of its operations, several of the global Pharma companies have publicly responded. Most notably among them, Novartis and GSK have targeted the removal of PVC and/or single-use plastics from their packaging as a key goal. Although the fine print has some exclusions for the necessity to protect human health, most Pharma multinationals are now actively trialling PVC-free blisters, and developing strategies to use them for new product launches.
In 2023, the 19 members of the Pharma Manufacturing Forum signed an Emissions Reduction Memorandum, to publicly declare their commitment to “scale collective action for positive change”, and to drive suppliers to do the same.
Added external commercial pressure has come from retailers across Europe, some of whom have indicated that they will eventually de-list products that are not in recyclable packaging. For example, Tesco, the largest supermarket chain in UK, has the target to make all packaging recyclable by the end of 2025. It is not clear whether this deadline will include its OTC products and in-store pharmacies, but this adds to the pressure on Pharma companies to comply. Those companies with a broader range of Consumer Health products, including OTC and VMS (Vitamins, Minerals and Supplements), such as Bayer, Reckitt and Haleon, are also among the leading drivers to switch the Pharma products away from PVC packaging, to avoid mixed messaging with their consumer brands.
Finally, as the EU PPWR comes into force, even if Pharma products are excluded from any deadlines, the parallel increase and eco-modulation of Extended Producer Responsibility (EPR) fees add a further financial incentive to reduce packaging costs by investing in sustainable packaging.
The suppliers of blister packaging have been equally active. Amcor, the largest supplier of aluminium foils for Pharma, declared in 2018 that 100% of its packaging would be recycle-ready by 2025, and they seem to be on target to meet this, including for Pharmaceutical blisters. The leading suppliers of PVC-based blisters, such as Klockner Pentaplast, Liveo Research, Tekni-Plex and Perlen Packaging were initially a little more circumspect in their approaches to this innovation, and have responded with various strategies, partly linked to their limited capabilities outside the manufacturing of PVC-based films.
This has given new entrants, most notably Etimex, already strong in PP blisters, and Südpack Medica space to exploit the need for PVC-free options, and to begin to establish a foothold in this emerging space. Other leading flexible packaging companies have used their expertise outside of Pharma to support this drive with the tricky challenge of replacing the foil lidding with a polymer option. Constantia Flexibles, adapa and Huhtamaki are among the manufacturers to team up with the producers of the base films to develop the lidding films for monopolymer blister packs.
Current Materials and Status
To understand the challenges and complexity the industry faces, it is necessary to look at the current status of development according to the level of moisture barrier.
Low Barrier
Furthest advanced is the low barrier blister, with 250µm PVC and a 20µm foil push-through lid as the most widely used incumbent format. It is unsurprising that PET and PP base films are leading this segment, as the technologies are long-established.
However, the biggest challenge of the past few years has been to produce a push-through film in PET and PP. Unlike a lacquered, hard-tempered aluminium foil, polymers tend to stretch, so creating a film that breaks at an appropriate force, without damaging the tablet or capsule, and leaving no particles has been a significant technical hurdle for the packaging innovators. Currently, the most common solution for PET lidding is to have a thicker film, around 30µm, and to use laser scoring to create a break line. At least one supplier has developed an 18µm film that breaks without scoring, which has certain advantages when it comes to printing, as well as saving additional weight. PP lidding options are available in various gauges from multiple suppliers without the need for scoring.
The push-through action is not the only challenge that has been faced. Printing of the medicine data is critical on the lidding, and ensuring sufficient contrast, and compatibility with existing ink systems and printing technologies, without compromising the recyclability, has also taken great effort on the part of the suppliers. As yet, the further problem of in-line digital printing and laser etching of the batch data has not been fully solved.
The first PET-based monopolymer blister pack was launched in November 2024 by Bayer, using films from Liveo Research.

The choice between low barrier PET and PP options is complex, as each has its own pros and cons. For example, the all-PET blister has an MVTR at least 4x higher than the PVC/Al blister. Whilst this may not be a problem for many drugs currently in a low barrier PVC blister, there will be some that fail shelf-life tests at this level, and this may cause Pharma companies to choose PP for their low-barrier needs, as a lower-risk option. The current all-PP specifications range from around 40-90% of the MVTR of PVC/Al, making it a safer choice for barrier.
MVTR is not the only criteria, and PET has a significant advantage over PP in terms of transparency. PP blisters are hazy in varying degrees, and, in particular for OTC and VMS products, this may not please the marketing teams. As Pharma blisters often use a white base film, translucency is less of an issue here.
Another aspect is the availability of recycling, which is simpler and more widespread for polyolefins (PP and PE) than for PET trays, especially in Europe, and may also therefore be in favour of PP.
The final consideration of the materials is the rigidity. PP is noticeably less rigid that PET and PVC after forming, which could create risk during the validation phase, with empty blisters more susceptible to denting. In practice, this risk is small, if the blister is optimally designed for the tablet.
Medium Barrier
In the medium-barrier range, the choices are currently more limited. The highest end of the new generation all-PP blisters reach MVTR levels approaching the level of PVC with 40-60gsm PVdC and foil lid. The all-PE blisters, such as AmSky from Amcor, have greater MVTR expectations, meeting the level of PVC with 60-90gsm PVdC and foil lid, and even approaching the barrier of 120gsm PVdC or 51µm PCTFE.
PE is visibly hazier than PP, but in the absence of highly transparent alternatives, the industry may have to accept this compromise. Similarly to PP, PE is also softer after forming compared to PVC. At time of writing, the PE mid-barrier solutions are furthest developed, and the PP producers are racing to catch up in this space.
Although there is a great deal of interest in medium-barrier all-PE blister from Pharma companies, it appears that a Consumer Health product in USA will be the first medium-barrier all-PE blister launch in the first half of 2025.
High Barrier
For medicines requiring high moisture barrier, today using PVdC coatings above 120gsm, and PCTFE gauges above 51µm, there are no recyclable monopolymer options in sight. The major limiting factor for the moisture barrier is the lidding, which inevitably has much greater transmission than the impermeable aluminium, and none of the suppliers have a recyclable solution on the horizon.
The additional complexity in this space is that PFAS regulations may restrict or even ban the use of PCTFE in the coming 5-10 years. Although discussions are still ongoing, there is already concern among Pharma companies about the use of PFAS as a primary packaging material for medicines, and there is evidence that some are planning to exit the use of PCTFE. If there is a significant shift away from PCTFE, this will have a major impact on the key suppliers, most significantly Honeywell, the producer of Aclar™ PCTFE films, and larger converters such as Klockner.
Given that there are no clear options for recyclable, high barrier polymer blisters, Pharma companies will have to make the strategic choices between:
- a continued use of high barrier PVC-based blisters
- using a medium-barrier blister and foil overwrap
- expanding the use of cold form blisters
- switching to HDPE bottles.
The Business Case for Monopolymer Blisters
In addition to the core considerations of the barrier performance and appearance of the blisters, there are several other criteria that Pharma companies must evaluate to build a successful business case for monopolymer blisters.
The major benefits are the reduction in weight, and in EPR fees vs PVC-based blisters. Figure 5 shows an analysis produced by Novartis in 2024 comparing the weight and EPR impact of PET and PP blisters. This analysis clearly shows benefits of both PET and PP, with the thinner PP specifications (PP 3,4,5) having the greatest advantage.

A second benefit is the reduction in carbon emissions, evaluated using Life Cycle Analysis methods. The same Novartis study demonstrates the benefits of both PET and PP vs PVC, with PP also having an advantage over PET.
This data is backed up by a similar analysis published by the Pharma Manufacturing Forum in February 2025, which additionally includes PE blisters at a comparable level to PP.

Weighed against these benefits are the total costs of monopolymer blisters. These costs are heavily dependent on the material base used, the supplier and volume. Whilst total costs may be higher today, it can be expected that costs for all monopolymer blisters will become more attractive as volumes and processing experience increase, against an expected increase in the cost of PVC blisters as volumes decline.
The second major cost element is the processing on blister lines. It is unlikely that blister lines can be dedicated to individual materials in the medium term, so the changeover cost, tooling costs, and production speed are all factors in the decision-making.
PET and PP/COC/PP both perform very similarly to PVC, have a wide processing window, and use the same tooling as PVC, so possess a clear advantage in terms of maximising processing performance. Both mono PP and PE require new tooling, as well as plug assist also being likely. The tooling is specific to each material, increasing both the changeover between batches, and the need to invest in new tooling. However, the extensive administrative time required between batch changeovers makes the physical tooling changeover less critical. Equally, as the industry introduces PVC-free blisters initially for new product launches, where an investment in new tooling is required in any case, this impact is likely to be minimal. Only if an existing drug is switched from PVC to PP or PE does the tooling cost become an important factor in the drug Lifecycle Management assessment.
The new generation of PP films, as well as PE films, have a reasonably wide operating temperature window for both forming and sealing. Although testing at high speeds is not yet extensive, the requirement of the Pharma companies and CDMOs is that processing speeds for PET, PP and PE on high-speed lines will need to be comparable to PVC. If this proves not to be true, the business case is significantly weakened.
Overall, testing to date indicates that the operational costs for all the PVC-free blister options are expected to be similar to their PVC barrier equivalent, reducing this factor as a hurdle to change.
At time of publication, the challenge of DOD printing has yet to be resolved on any of the polymer lidding films, with laser-scored PET possibly at higher risk of damage during the DOD printing. Experience suggests that it is a matter of time before suppliers find a solution for this.
Weighing up these factors to evaluate and select the various options will depend upon the Pharma company’s strategic priorities, product mix, and internal cost structure, amongst others.
Figure 6 shows the comparative level of moisture barrier of the current range of closed blisters, comparing monopolymer blisters against the PVC-based equivalent with Al foil lid. This highlights the PVC-free opportunities for low- and medium-barrier, with all-PET, all-PP, PP/COC/PP and all-PE blisters providing several options for Consumer Health and Pharma companies.
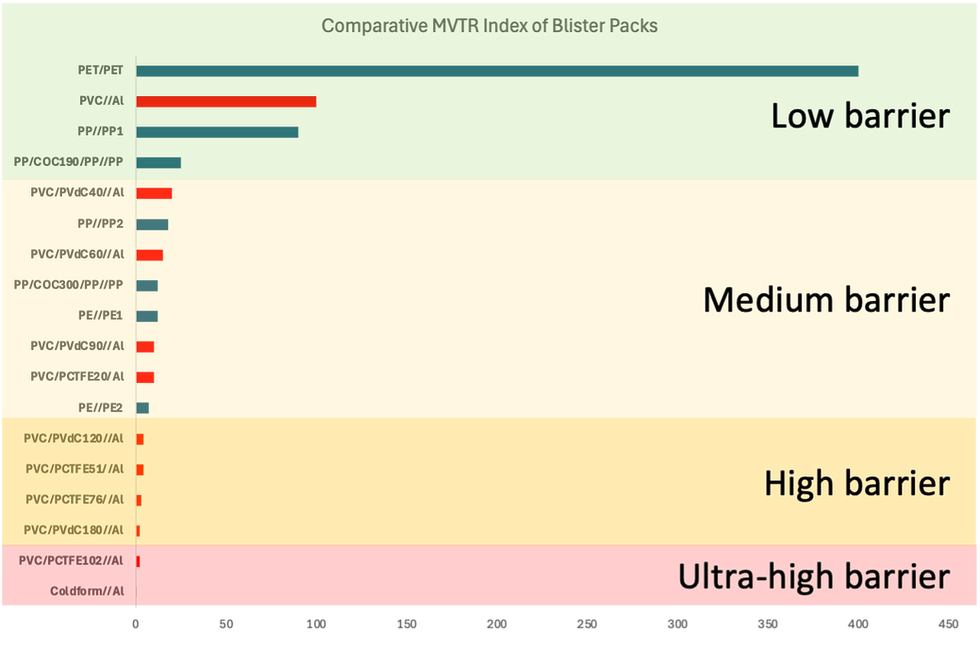
There appear to be no PVC-free polymer options in the higher-barrier range in sight. Although this segment represents less than 5% of the total blister demand globally, considering Pharma, OTC and VMS applications, it is 15-20% of the total usage for Pharmaceutical applications in Europe and North America, and will therefore be a challenge for many Pharma companies.
What does this mean for PVC?
It is evident that major Pharma companies are committing significant resources to testing PVC-free blisters, and the launch of Bayer Aleve in an all-PET blister in November 2024, together with the imminent launch of a Consumer Health product in an all-PE blister in US, have taken away the first-mover risk. As the monopolymer specifications are fine-tuned and stabilised, it is reasonable to assume that more products will be launched in PVC-free blisters in the coming years, perhaps even the vast majority from 2030 onwards.
The business case to switch existing products from PVC/Al to monopolymer is not yet as strong, and Pharma companies will have to be more selective about this. As products age, Lifecycle Management considerations will determine when it becomes economically attractive to replace the PVC blister packs with the PVC-free alternative.
The ongoing developments, and economic assessments suggest that the impact on PVC volumes will likely be limited up to 2030, with general growth in demand outweighing the growth in PVC-free options. It is foreseeable that a noticeable change will begin in earnest from around 2030, with new product volumes increasing, and more and more older products switching away from PVC.
Although driven primarily by European issues, there will be a knock-on effect across other regions, as global Pharma companies will prefer to take a standardised approach.
It can be expected that PVC will still be in use for a minority of blister packs in 2040 and beyond, but as volumes decrease, costs will increase, and the attractiveness of PVC blisters diminishes further.
Predicting how much PVC will continue to be used, and which of the recyclable materials will replace it, is somewhat of a guessing game. It is possible to consider different models with some broad assumptions of growth and speed of change, to identify the best- and worst-case scenarios for the suppliers of recyclable blister materials, as well as the challenges to be addressed by the PVC producers.
Figure 7 makes some assumptions about the future global growth in demand for blister packaging, and two possible scenarios for the speed and extent of the transition to PVC-free blisters. The model assumes a baseline growth in demand of 1-3% CAGR, varying by region. Scenario 1 shows a slower growth of the use of PVC up to 2030, then a gradual transition away from PVC from 2030, accelerating to 5-10% p.a. after 2035. This results in the PVC demand in 2040 being around 70% of the 2025 level, and 50% of the baseline level. Scenario 2 is a faster transition after 2030, 10% to 20% p.a., which results in PVC demand in 2040 being 35% of the 2025 level, and only 25% of the baseline level.

Without predicting the mix of PET, PP and PE blisters, the model assumes that the average weight of the base film is 75% of PVC, and the lid film is 20% of that. The two scenarios show a demand in PVC-free blisters, including both the base and lid films, of between 200,000 tonnes and 300,000 tonnes by 2040.
Compared to the baseline level, the total annual reduction in the use of PVC by 2040 is 250,000 to 350,000 tonnes, and the net weight saving in plastic packaging is 25,000 to 35,000 tonnes. In addition to this, the replacement of the aluminium foil lid is a further annual saving of between 50,000 and 80,000 tonnes in 2040, giving a total weight saving of blister packs of 75,000 to 115,000 tonnes annually, compared to the baseline.
Whilst these models are estimates, they highlight the enormous potential of the move to PVC-free blisters for the Pharmaceutical industry, as well as the opportunities for the suppliers of PVC-free blister materials.
Equally, they throw up several challenges for the current suppliers of PVC blister packaging and aluminium lid foil. The models suggest that in Europe, only 20% to 50% of the current PVC production will be needed in 2040. For aluminium lid foil, considering continued growth in cold form blisters, the global impact would be a reduction of between 10% and 35% of demand by 2040.
Further Challenges to Overcome
Solving the technical problems of the primary packaging has been a major success story for the packaging suppliers, as well as the commitment of Pharma companies. Whilst this is the critical enabler to make blister packs recyclable, it does not ensure that they will actually be recycled in large numbers.
The disposal and collection of used blister packs are larger problems of society and infrastructure that still require much work. As a blister pack may contain unused tablets or residual pharmaceutical content, will it be sufficient for finished packs to be included in the general recycling collection? If not, collection centres may be needed at pharmacies, supermarkets and other outlets, which will likely limit the percentage of packs that are recycled.
Chemical recycling is making significant advances, to break down polymers into their component chemicals, allowing the re-creation of the uncontaminated polymer. With this key step, it may then be possible for chemically recycled polymers to re-enter the pharmaceutical packaging production chain without risk. This is a big step for the regulatory bodies to decide on. As shown by the investment of Südpack, chemical recycling may also be an opportunity for packaging companies to help accelerate and benefit from this innovation.
Summary
It seems that the tide has turned on recyclable blister packs, and their widespread adoption will soon be a reality.
This change is being embraced by Pharmaceutical and Consumer Health companies in Europe and elsewhere, and the packaging industry has demonstrated its ability to innovate and meet the demanding and complex challenges.
Monopolymer blisters are available in PET, PP and PE, covering the low- to medium-barrier range, with new products now being launched. The extent and timing of the move from PVC will become more apparent in the next 3 to 5 years, however, it seems inevitable that the adoption of PVC-free blisters will mean significant changes for existing suppliers and new ones.
The continued need for high barrier solutions will likely see a continued usage of PVC for decades to come, but it seems inevitable that the majority of thermoform blisters will be packed in recyclable polymers in 10 to 15 years.
With annual savings in packaging weight of over 100,000 tonnes, and the potential to have at least 75% of all thermoform blisters made with recyclable polymers, the prize is valuable for the industry, and one that it is now keen to reach.
For the packaging industry, it will require existing suppliers of PVC/Al blisters to invest in major changes in their operations, and new suppliers to manage a steep learning curve.
This may lead to structural changes in the competitive landscape, with several major initiatives already seen; Perlen Packaging acquiring LOG Pharma Packaging, perhaps partly in anticipation of a greater demand in high barrier bottles; various collaborations, such as Perlen and Etimex, Klockner and Huhtamaki, Liveo and adapa, Südpack and Liveo, to expand product ranges and co-market recyclable solutions.



Fig. 8 Monopolymer blister packs
Left to right: Klockner R1 (PET), Südpack Pharmaguard (PP), Amcor AmSky (PE)
The subsequent steps to improve the disposal and collection of blister packs, and the increased use of chemically recycled polymers as raw materials, will demand further collaborations across the industry, including the regulatory bodies, who will need to support these advances.
References and Data Sources:
Novartis, Südpack Medica, Amcor Flexibles
Pharmaceutical Manufacturing Forum
EU PPWR
EUROPEN Factsheet on EPR for used packaging
Various Pharmaceutical and packaging company websites and data sheets
Image Credits:
Amcor, Klockner Pentaplast, Südpack, Etimex, Huhtamaki, adapa, Bayer, Museum of New Zealand
Glossary of terms and abbreviations used in this document:
EU PPWR The EU Packaging and Packaging Waste Regulations
EPR Extended Producer Responsibility: regulations to encourage product owners to
take responsibility for their product packaging by rewarding good design and charging fees for poor design
PFAS Per- and polyfluoroalkyl substances: used to improve water and chemical resistance
DEHP Di(2-ethylhexyl) phthalate: used to make plastics more flexible
PVC Polyvinyl chloride
PET Polyethylene terephthalate (a form of polyester)
PP Polypropylene
PE Polyethylene
COC Cyclic olefin copolymer
Polyolefin A class of polymers including PP, PE and COC
PVdC Polyvinylidene chloride: a coating applied to PVC to improve barrier to moisture & oxygen
PCTFE Polychlorotrifluoroethylene: applied as a film laminated to PVC to improve moisture barrier
MVTR Moisture vapour transmission rate (measured in g/m2/day)
OTC Over the counter: medicines that do not require a prescription
VMS Vitamins, minerals and supplements (also commonly referred to as nutraceuticals)
CH Consumer Health: a broad term including OTC and VMS products
Al Aluminium foil
Comments